Self-build energy efficiency drives dramatic cost savings
Building an energy-efficient home in the UK now costs just 8% more than standard construction, yet delivers 90% reductions in heating demand and annual energy savings of £600-£800. The convergence of tightening regulations, mature supply chains, and proven technologies makes 2025 a pivotal year for self-builders to embrace high-performance construction, with the Future Homes Standard mandating heat pumps and enhanced fabric efficiency for all new builds.
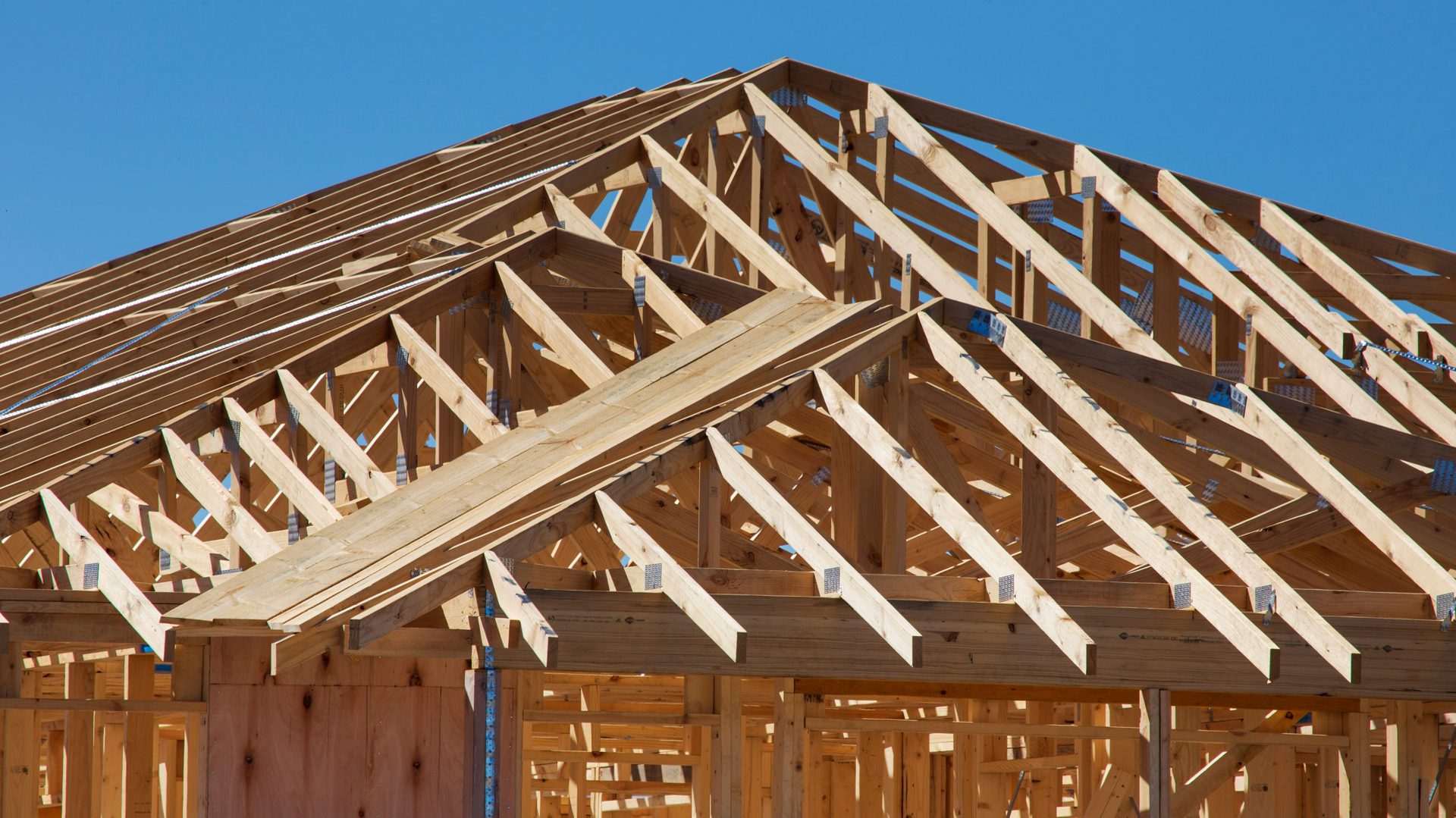
Energy-efficient self-builds represent the intersection of regulatory compliance, long-term cost savings, and superior living comfort. Current UK Building Regulations Part L already require significant improvements over previous standards, including U-values of 0.18 W/m²K for walls and air permeability below 8 m³/(h·m²)@50Pa. The upcoming Future Homes Standard 2025 will mandate 75-80% carbon reductions, effectively requiring heat pump installation and enhanced building fabric. For self-builders starting projects now, understanding and exceeding these standards offers both immediate planning advantages and long-term financial benefits, with payback periods typically ranging from 6-10 years based on current energy prices.
Passivhaus principles transform UK self-build economics
The Passivhaus standard, once considered exotic and expensive, now achieves certification for approximately £2,000-£2,200 per square meter in the UK market. This represents just £130-£180 per square meter above standard construction costs, a premium that continues to decrease as the supply chain matures. The five core Passivhaus principles—ultra-low heating demand (≤15 kWh/m²/year), exceptional airtightness (≤0.6 air changes per hour), high-performance insulation, triple-glazed windows, and mechanical ventilation with heat recovery—create homes that use 90% less energy for heating than typical UK buildings.
UK-specific climate data, available through 22 regional datasets in the Passivhaus Planning Package (PHPP), enables precise modelling for locations from Northolt to Inverness. The certification process, managed by the Passivhaus Trust UK and independent certifiers, costs £3,000-£8,000 depending on project size. Critically, the UK’s moderate climate proves ideal for Passivhaus construction, with lower cooling demands than continental Europe and achievable comfort levels year-round. Recent projects like the Suffolk Richardson house (£2,059/m², Build It Awards 2023 winner) demonstrate that Passivhaus certification delivers both prestige and performance within realistic budgets.
Planning authorities increasingly view Passivhaus projects favourably, with some councils offering fast-track approvals. Conservation areas and even Green Belt sites have approved Passivhaus designs based on their sustainability credentials. The UK supply chain now offers comprehensive product availability, from triple-glazed windows (£400-£800/m² from suppliers like Green Building Store and Internorm) to certified MVHR systems from Zehnder, Brink, and Vent-Axia. Self-builders report that early integration of Passivhaus principles during design saves 60% of the potential cost premium compared to retrofit approaches.
Building physics fundamentals guide “fabric-first” success
Understanding heat loss calculations and moisture management underpins successful energy-efficient construction. The UK’s Standard Assessment Procedure (SAP 10.2) calculates dwelling performance, with approved software costing around £1,000 for certification. Current Building Regulations mandate maximum U-values of 0.28 W/(m²K) for walls, though the notional building standard achieves 0.18 W/(m²K), indicating the performance level needed for compliance.
Thermal mass strategies work particularly well in southern England for overheating mitigation, though the Building Research Establishment notes that only the first 100mm of mass effectively participates in daily temperature cycles. Condensation risk analysis, traditionally using the Glaser method, increasingly requires advanced hygrothermal simulation through tools like WUFI Pro to account for driving rain, air leakage, and thermal bridging effects. Modern construction must balance insulation performance with moisture management, particularly given the UK’s high rainfall and humidity levels.
Airtightness is basically the critical factor linking insulation effectiveness with indoor air quality. While Building Regulations permit up to 10 m³/h/m² @ 50Pa, achieving below 3 m³/h/m² enables effective MVHR operation and significant energy savings. Testing costs £300-600 per dwelling, with progressive testing during construction recommended for high-performance targets. Common failure points include floor-wall junctions, service penetrations, and window installations, all addressable through careful detailing and quality products from suppliers like Ecological Building Systems (Pro Clima range) and similar specialist providers.
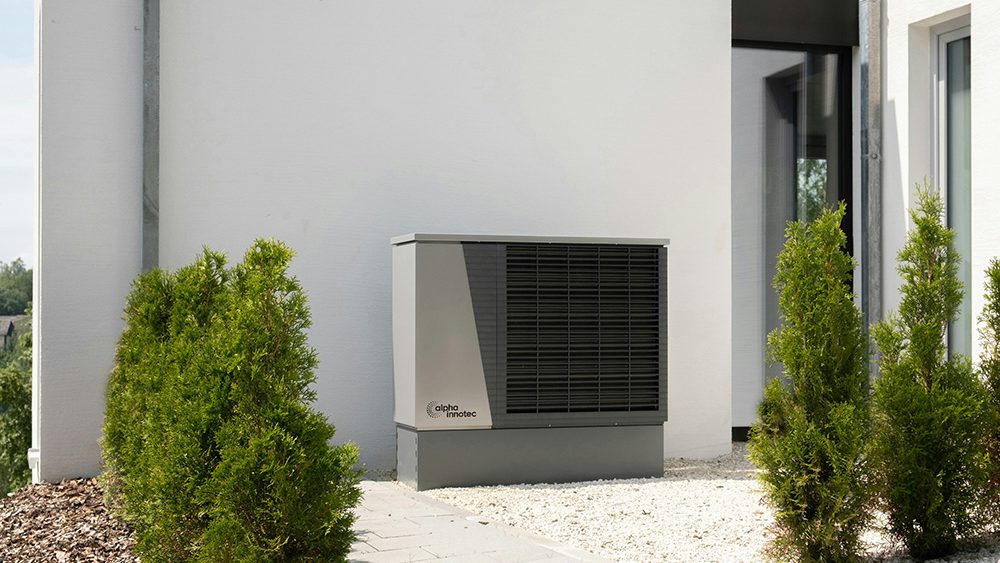
MVHR systems are essential for efficient ventilation
Mechanical Ventilation with Heat Recovery (MVHR) systems recover 75-90% of heat from exhaust air while providing continuous fresh air supply. Complete installed systems for a typical 150m² home cost £8,000-£15,000, including design, equipment, ducting, and commissioning. Market-leading Zehnder ComfoAir units achieve 96% efficiency but command premium prices (£2,500-£3,500 ex VAT), while mid-range options from Vent-Axia and Nuaire offer good performance at £800-£1,500.
System sizing requires careful calculation based on 0.3 l/s/m² general ventilation rates per Building Regulations Part F, with units ideally operating below 50% capacity for quiet operation. Professional design proves essential, costing £550+VAT but ensuring proper duct sizing, minimal pressure drops, and effective room-by-room ventilation. Installation typically takes 5-6 days, with semi-rigid ducting reducing installation time by 70% compared to rigid systems.
Annual running costs average £156 for electricity consumption (300kWh/year), with filter replacements adding £25-£125 annually. Professional maintenance runs £150-£300 per year, though many tasks suit competent DIY maintenance. The systems integrate well with heat pumps, reducing heating demand by up to 50% and enabling smaller heat pump sizing. Modern units offer smart controls, summer bypass modes, and optional heating/cooling modules, making them suitable for year-round comfort in the changing UK climate.
Thermal bridging elimination demands detailed design
Thermal bridges—areas where heat escapes more readily through the building fabric—significantly impact overall performance. Common problem areas include window and door installations, floor-wall junctions, roof-wall connections, and service penetrations. The UK’s default Y-value penalty increased from 0.15 to 0.2 W/m²K under Part L 2021, making thermal bridge elimination more critical for compliance.
Different construction methods offer varying solutions. Timber frame construction benefits from external insulation layers with 33% of thermal resistance outside the frame, while masonry construction using aircrete blocks and continuous cavity insulation minimizes bridging. Insulated Concrete Forms (ICF) and Structural Insulated Panels (SIPs) inherently eliminate most thermal bridges, achieving Y-values as low as 0.025 W/m²K with proper detailing.
Calculating thermal bridges requires 2D modelling software and adherence to BS EN ISO 10211 standards, with professional calculations costing £500-2,000 per project. Temperature factors (fRsi) must exceed 0.75 to prevent condensation risk. While Accredited Construction Details previously provided standard solutions, current projects require individual calculations, emphasizing the importance of early thermal bridge consideration in design. Construction premiums for enhanced details typically add 2-5% to project costs but often prove more cost-effective than alternative compliance routes like additional photovoltaics.
Achieving airtightness requires a systematic approach
Passivhaus-level airtightness (≤0.6 ACH @ 50Pa) demands comprehensive planning and quality execution. Pro Clima’s intelligent membranes and tapes, distributed by Ecological Building Systems, lead the UK market with 100+ year verified lifespans. Intello Plus membrane costs £3-5/m², with Tescon Vana tape at £8-12/linear meter providing robust connections. Window and door sealing using three-layer systems—weathertight, insulation, and airtight—prevents the majority of air leakage paths.
Testing procedures follow BS EN 13829 standards, with costs ranging from £190-450 for single dwellings. Progressive testing during construction enables remediation before finishes hide problem areas. Common weak points require specific solutions: service penetrations use Stoppa plugs (£2-10 each), intermediate floors need careful rim joist sealing, and window installations demand specialized tapes like Contega Solido SL (£15-25/linear meter).
Construction sequencing proves critical—installing the airtight layer early, protecting it during subsequent trades, and conducting multiple tests ensures final performance. UK self-build forum members consistently emphasize that achieving sub-1.0 ACH levels requires obsessive attention to detail but delivers substantial comfort and energy benefits. The total material cost for comprehensive airtightness measures typically adds £2,000-£4,000 to a project, with labour costs varying based on contractor experience.
Future Homes Standard 2025 reshapes construction requirements
The Future Homes Standard, implementing in 2025, mandates 75-80% carbon reductions compared to pre-2022 levels. Two options under consultation offer different pathways: Option 1 requires air source heat pumps with solar PV at £10,000-£15,000 additional cost, while Option 2 mandates heat pumps only at £5,000-£8,000 premium. Gas boilers face effective prohibition in new builds from 2025, making heat pump readiness essential for current projects.
Current Part L 2022 already requires significant improvements, with notional building specifications including triple glazing, enhanced U-values, and air permeability below 5 m³/(h·m²)@50Pa. Self-builders starting now should exceed these standards to avoid costly retrofits—targeting U-values 30% better than minimum requirements typically adds just 3-5% to construction costs while future-proofing the build.
Government support includes the Boiler Upgrade Scheme offering £7,500 grants for heat pump installation, Help to Build equity loans up to 20% of project costs, and 0% VAT on new build materials. The Home Energy Model will replace SAP calculations from 2025, requiring updated assessment approaches. Planning for low-temperature heating systems, adequate plant room space, and robust building fabric ensures compliance without last-minute specification changes that inflate costs.
Real project data reveals improving economics
Recent UK self-build projects demonstrate rapidly improving economics for high-performance construction. MVHR installations average £6,450 including equipment and labour, with Zehnder systems commanding 100% premiums over budget alternatives but delivering 90% efficiency versus 57% for basic units. Triple glazing costs £440-£1,430 per window, representing just 10-20% premiums over high-quality double glazing while dramatically improving comfort and energy performance.
Payback calculations show compelling returns: heat pumps typically achieve 6-year ROI when replacing electric heating, saving £830-£1,400 annually. Passivhaus builds recover their 8% construction premium within 10 years through energy savings alone, while adding approximately 10% to property values according to market research. A 200m² Passivhaus home achieves annual heating bills of just £90 using heat pump technology, compared to £1,434 for average UK homes.
Case studies highlight successful approaches: RDA Architects delivered a £250,000 three-bedroom Passivhaus using cavity wall construction, proving high performance achievable on modest budgets. PH15 consultants achieved 0.07 ACH@50Pa airtightness with integrated solar arrays for net-zero energy performance. Common mistakes include late-stage cost cutting that compromises airtightness, poor MVHR commissioning reducing efficiency, and thermal bridge details overlooked during construction. Self-builders consistently report that engaging specialist designers early and maintaining quality focus throughout construction delivers both performance and value.
Comprehensive strategy ensures energy efficiency success
Creating a successful energy-efficient self-build requires integrated planning from concept through completion. Begin with clear performance targets—whether Passivhaus certification, AECB Silver standard (40 kWh/m²/year), or simply exceeding Building Regulations by comfortable margins. Engage qualified professionals early: Passivhaus designers for PHPP modelling (£2,000-£2,800 for training if doing it yourself), SAP assessors for compliance (£400-£800), and experienced contractors familiar with airtightness requirements.
Budget realistically for the performance level desired. Current construction costs range from £1,750-£3,200 per m², with high-performance builds adding 8-15% premiums that deliver 6-10 year paybacks. Factor in professional fees, testing costs, and contingencies for remedial work. Quality installation proves more critical than component specification—the best triple glazing performs poorly if badly fitted, while modest systems professionally installed can exceed expectations.
Product selection should prioritize proven performance over marketing claims. For MVHR, Zehnder and Brink lead on quality and efficiency, while Vent-Axia offers good value. Window suppliers like Green Building Store and Norrsken specialize in high-performance glazing with comprehensive technical support. Insulation and airtightness products from Ecological Building Systems provide certified performance with long-term warranties. Lead times vary from 1-2 weeks for MVHR systems to 4-8 weeks for bespoke glazing, requiring careful project scheduling.
Expert planning delivers exceptional homes – get OCD about it
UK self-builders now access mature supply chains, proven technologies, and supportive regulations that make energy-efficient construction both achievable and economically attractive. The convergence of rising energy costs, tightening standards, and growing climate awareness creates optimal conditions for high-performance builds. Whether targeting Passivhaus certification or simply exceeding Building Regulations, the key lies in early planning, integrated design, and uncompromising attention to quality during construction.
Success requires balancing multiple factors: technical performance, regulatory compliance, construction costs, and long-term value. By understanding building physics principles, specifying appropriate systems, eliminating thermal bridges, achieving excellent airtightness, and preparing for future standards, self-builders create homes offering superior comfort, minimal running costs, and lasting value. The 8-10% premium for high-performance construction returns through energy savings within a decade while delivering daily benefits in comfort, air quality, and climate resilience.
Start with professional guidance, maintain quality focus throughout construction, and view energy efficiency investments as essential infrastructure rather than optional extras. The UK’s path to net-zero requires today’s self-builders to embrace these standards, with early adopters benefiting from planning advantages, grant support, and the satisfaction of creating truly sustainable homes. The question is no longer whether to build efficiently, but how ambitiously to exceed minimum standards for maximum long-term benefit.