The ultimate guide to self-build materials selection
Creating a self-build home requires navigating thousands of material choices that impact everything from structural integrity to energy efficiency and final costs. This comprehensive research reveals current UK market pricing, performance data, and critical decision factors across seven major material categories, identifying key opportunities to help self-builders make informed choices while avoiding costly mistakes.
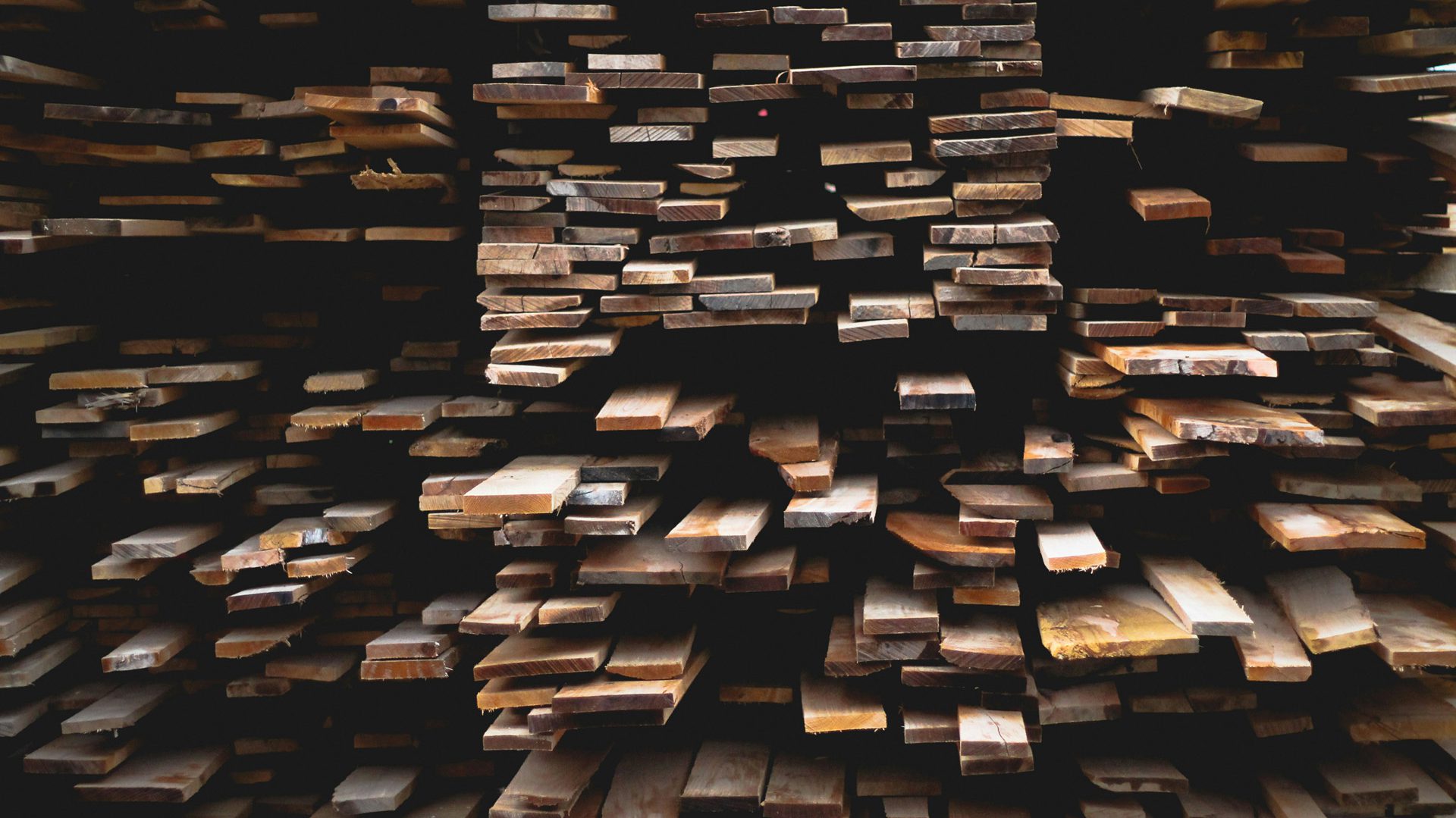
Foundation systems anchor both budgets and buildings
Foundation costs typically consume 15-30% of total build budgets, making early decisions crucial for project viability. Strip foundations remain the most cost-effective option at £95-115 per linear meter for machine excavation, suitable for stable ground conditions with bearing capacity above 75kN/m². However, challenging sites may require raft foundations (£200-260/m²) or piled solutions (£250-300/m² total cost), dramatically impacting budgets.
The most expensive self-builder mistake is inadequate ground investigation. A £1,200-1,800 soil survey can prevent foundation costs spiralling from an expected £7,000 to £30,000+ when unexpected ground conditions emerge. Building Regulations Part A requires minimum 1000mm depth, but tree proximity in clay soils can demand foundations up to 3000mm deep.
Major concrete suppliers like Cemex, Heidelberg Materials, and Tarmac charge £130-150/m³ delivered, with minimum order charges of £625+VAT typical. VAT reclaim through the DIY Housebuilders’ Scheme can recover 15-20% of material costs, making proper documentation essential from project start.
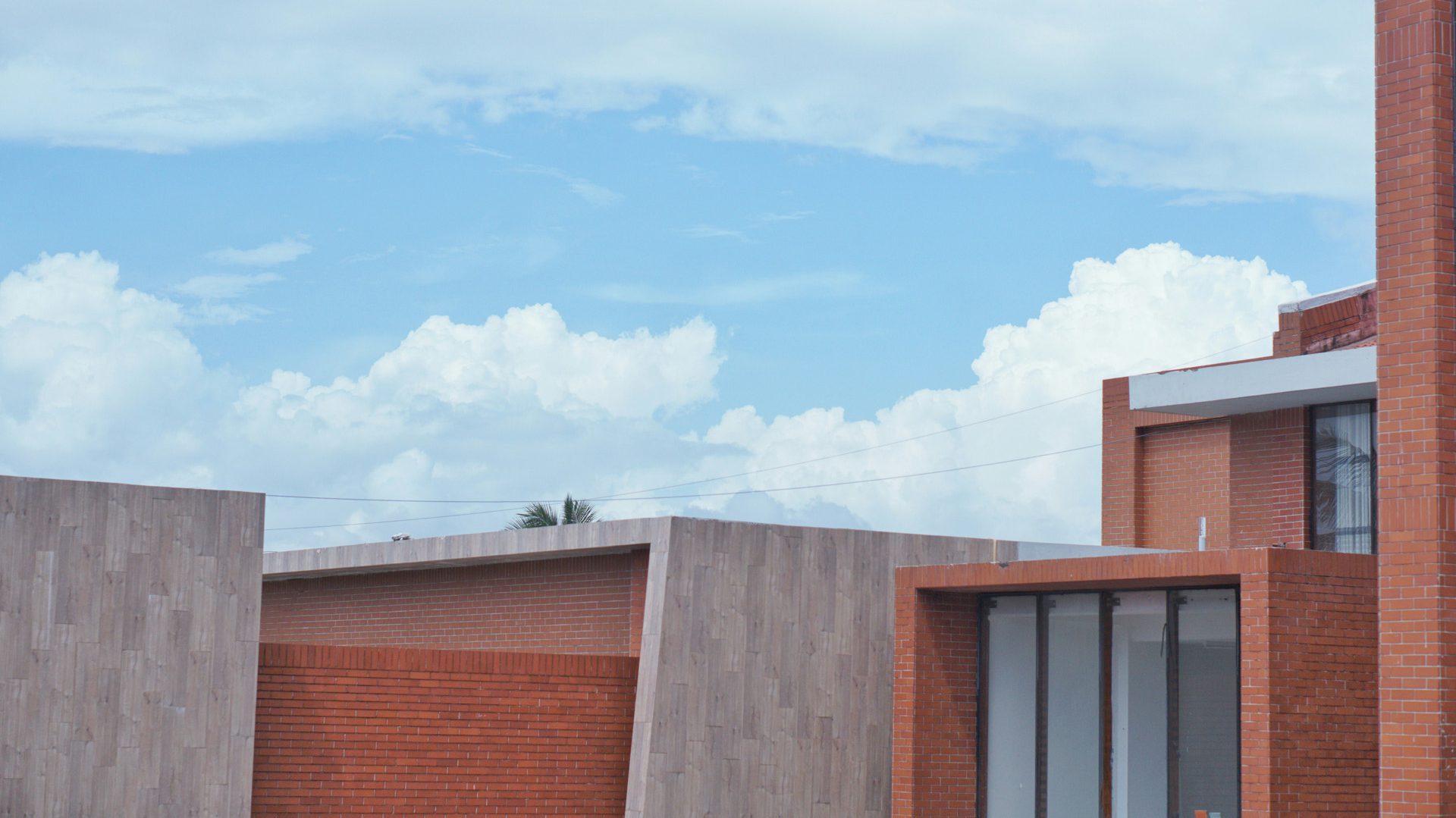
External wall systems balance speed, performance, and tradition
Wall system selection profoundly impacts build timeline, thermal performance, and aesthetic outcomes. While masonry construction costs £80-100/m² for materials, timber frame (£72/m² structural only) can reduce a 20-week build to just 1-2 weeks for weathertight shell completion. Total build costs across all systems converge at £1,300-1,700/m², making performance and speed often more important than pure material costs.
Timber frame dominates the speed category, with companies like Potton offering complete homes from £187,000-328,000. ICF (Insulated Concrete Forms) from suppliers like Nudura achieve exceptional airtightness below 1 m³/h.m² while combining insulation and structure in one system. SIPs panels from Kingspan TEK enable 3-day shell completion with U-values suitable for Passivhaus standards.
The 2021 Building Regulations Part L mandates 0.18 W/m²K maximum U-values for walls, with mandatory airtightness testing at 8 m³/(h.m²) maximum. All systems can meet these requirements, but timber frame and SIPs excel at exceeding them cost-effectively, particularly important as regulations tighten further by 2025.

Roofing materials span a centure of lifespan differences
Roofing material selection impacts structural requirements, longevity, and significant aesthetic considerations. Spanish slate at £60-95/m² offers the best performance-to-cost ratio, while Welsh slate commands premium prices of £65-160/m² but delivers 75-150+ year lifespans. Concrete tiles from Marley and Redland (£20-45/m²) provide reliable budget options with 40-60 year lifespans.
Weight considerations prove critical: clay tiles at 45-55 kg/m² may require structural reinforcement, while modern metal roofing weighs just 4-8 kg/m², enabling retrofits without strengthening. Green roof systems at £50-100/m² for extensive sedum types add 70-300 kg/m² but provide biodiversity, insulation, and stormwater management benefits increasingly valued by planners.
Installation costs vary dramatically by complexity. Basic concrete tile installation adds £12-20/m² labor, while natural slate demands skilled craftsmen at £25-40/m². Regional preferences matter: conservation areas often mandate matching existing materials, while exposed coastal locations favor aluminum or treated steel for corrosion resistance.
Windows and doors determine both comfort and running costs
The glazing specification impacts long-term energy costs more than any other envelope component. Triple glazing now costs just 20-50% more than double (£660-4,320 per window versus £600-3,600) while delivering U-values of 0.7-1.0 W/m²K compared to 1.4-1.6 for double glazing.
Frame material choices span wide price ranges: uPVC averages £250-640 per window supply-only, timber runs £415-680/m², and aluminum costs £475-568/m². Composite frames at £520-620/m² combine timber’s thermal performance with aluminum’s durability, increasingly popular for premium builds. Whole-window U-values matter more than center-pane values, with poor installation potentially doubling effective U-values.
Green Building Store and Velfac supply Passivhaus-certified windows achieving 0.8 W/m²K or better. For standard builds, quality uPVC with enhanced glazing provides excellent value, while exposed locations benefit from triple glazing’s superior performance despite higher initial costs.
Insulation technology drives energy performance gains
Building Regulations Part L requires U-values of 0.18 W/m²K for walls and 0.11 for roofs in new builds. PIR boards from Kingspan and Celotex at 0.022 W/mK thermal conductivity offer the thinnest solutions at £15-40/m², while mineral wool at £3-15/m² provides cost-effective performance with superior fire safety.
Natural alternatives gain market share despite 20-50% price premiums. Thermafleece sheep’s wool (£12-25/m²) manages moisture naturally, absorbing 30% of its weight while maintaining performance. Wood fiber insulation from Steico and Pavatex (£18-35/m²) adds thermal mass benefits, reducing summer overheating by 25-33%.
Recent price volatility saw PIR boards increase 40-59% over the past year, making mineral wool increasingly competitive for projects not constrained by thickness. Passivhaus projects typically require 300-400mm wall insulation and 400-500mm in roofs, achievable with any material but most space-efficient with phenolic foam products at 0.018-0.020 W/mK.
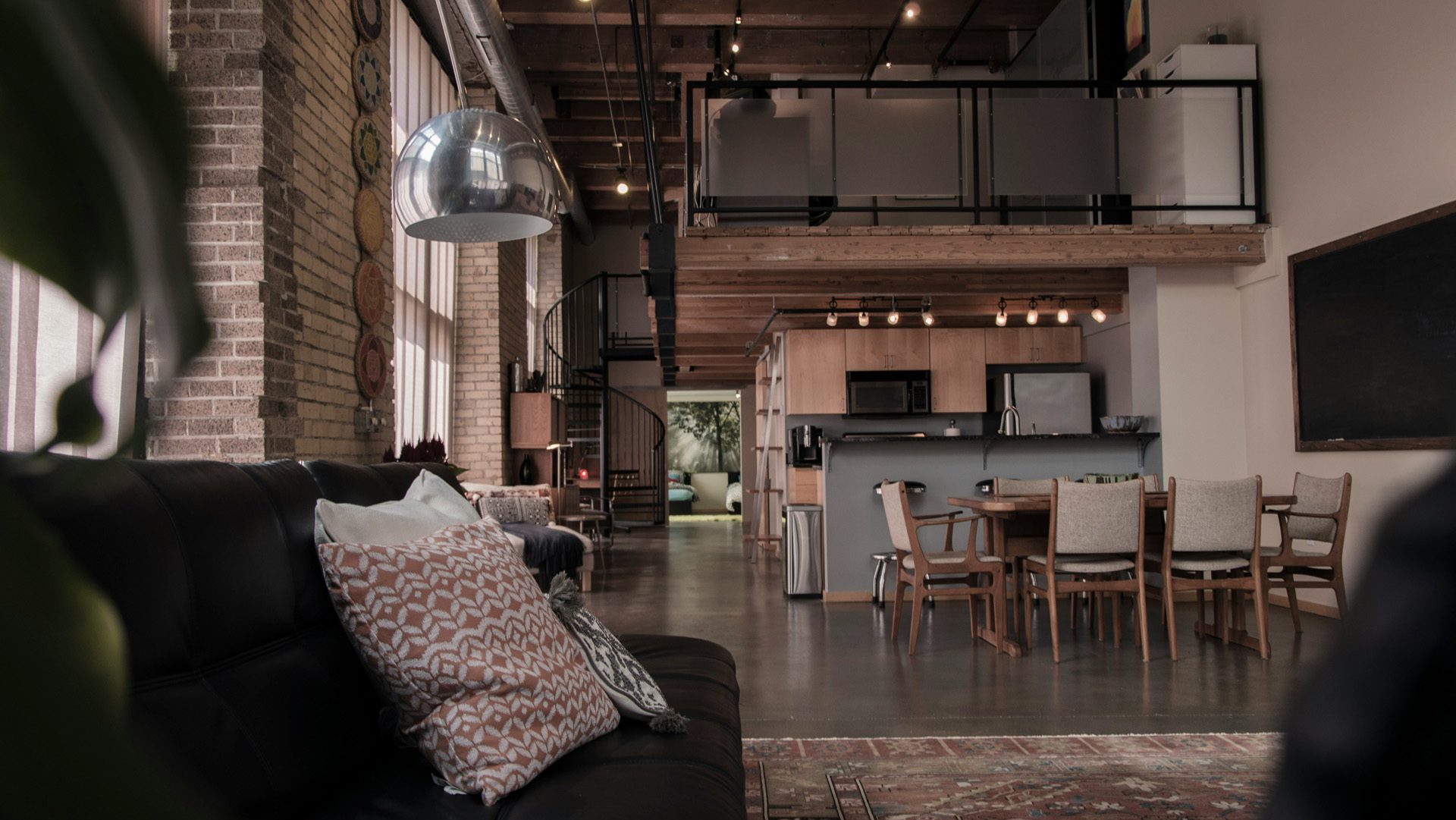
Internal finishes reflect lifestyle but also maintenance preferences
Flooring selection balances durability, maintenance, and upfront costs across dramatic ranges. Engineered wood at £60-75/m² installed offers 20-25 year lifespans with refinishing potential, while quality LVT at £32-90/m² provides waterproof, low-maintenance alternatives lasting 15-20 years. Carpet remains popular for bedrooms at £15-80/m² total cost but requires replacement every 5-15 years.
Wall finishes see significant labor cost components: plastering runs £8-13/m² for skim coating over plasterboard, with full wet plastering to masonry costing £600-1000+ per room. Paint selection impacts long-term maintenance, with Dulux Trade Diamond Matt at £49.99/2.5L offering superior durability over budget options, though Leyland Trade at £15/2.5L provides excellent coverage for tight budgets.
The DIY Housebuilders’ VAT reclaim scheme covers materials incorporated into the structure, potentially saving 20% on eligible finishes. Keeping detailed receipts throughout the project enables claims within six months of completion, often recovering £2,000-5,000 on internal finishes alone.
Sustainable materials = modest premiums for significant benefits
Environmental considerations increasingly influence material selection, with embodied carbon data from the ICE Database informing decisions. Hempcrete at £1,800-2,200/m² of floor area costs similarly to high-performance conventional systems but achieves carbon-negative construction while maintaining 16-18°C year-round without heating.
CLT (Cross Laminated Timber) at £30-50/m² for panels enables rapid construction with 40-60% lower embodied carbon than steel or concrete alternatives. Straw bale construction costs just £650/m² for self-builders, providing exceptional insulation at 2-3 times Building Regulations requirements with over two hours fire resistance.
UK suppliers specializing in sustainable materials include Green Building Store, Ecological Building Systems, and Mike Wye & Associates. While sustainable materials typically carry 10-30% premiums, operational energy savings of 20-50% combined with superior indoor air quality increasingly justify the investment. Both FSC and PEFC certification schemes meet UK government requirements for sustainable timber.
Strategic recommendations for materials selection success
The research reveals clear patterns for optimizing self-build material choices. Foundation decisions require early soil investigation to prevent budget overruns. Wall system selection should prioritize build speed and performance over minor cost differences. Natural slate and quality concrete tiles offer best roofing value, while triple glazing pays dividends in exposed locations.
For insulation, balance thickness constraints against cost, with PIR boards optimal for space-limited applications and mineral wool providing fire-safe economy. Internal finishes should match lifestyle requirements, with engineered wood and LVT offering best long-term value. Sustainable materials increasingly compete on total cost while delivering superior environmental performance.