The Complete Guide to Project Management Strategies for Self-Builders
For UK self-builders, the choice between acting as your own main contractor or hiring a professional can save or cost tens of thousands of pounds. Our research reveals that over 50% of UK self-builders choose self-management, achieving average savings of 17-25% on total build costs. However, this comes with significant responsibilities: you’ll need 20-30 hours per week during active construction phases, comprehensive insurance coverage, and the ability to coordinate multiple trades while ensuring CDM compliance. Whether you choose self-management, hire a main contractor, or adopt a hybrid approach, this comprehensive guide provides the frameworks, tools, and real-world insights needed to deliver your project successfully.
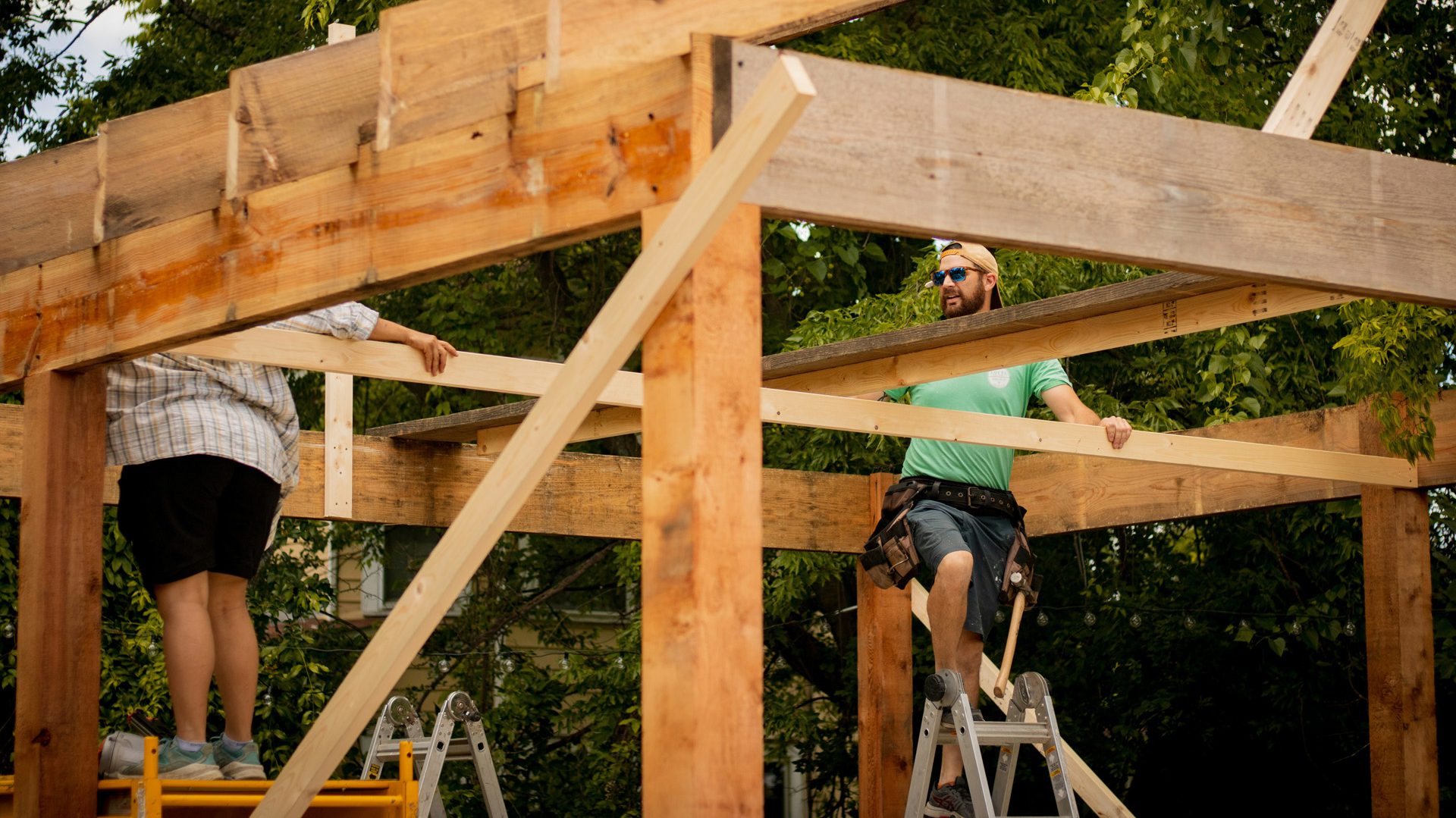
The project management landscape for UK self-builds
The UK self-build sector has evolved significantly, with sophisticated project management tools now available at every budget level. Modern self-builders benefit from cloud-based software starting from free options like ClickUp, to professional solutions costing £30+ per month. The most successful projects combine digital project management with traditional milestone planning, achieving completion rates 23% higher than those relying on manual methods alone.
Recent data from UK self-build forums shows that project management approach directly correlates with both cost control and completion time. Self-managed projects typically run 10-15% longer than professionally managed builds but deliver genuine cost savings when properly executed. The key differentiator isn’t choosing between approaches but matching your skills, time availability, and risk tolerance to the right management strategy.
Acting as your own main contractor
Understanding the legal framework
As a self-managing UK self-builder, you’re not technically becoming a contractor in the legal sense. Under CDM Regulations 2015, domestic clients typically see their duties transfer to contractors. However, when you control how work is carried out, you assume significant responsibilities. The HSE expects “coordination rather than supervision” – you coordinate trades but don’t supervise their technical work.
Essential legal requirements include:
- Public liability insurance (£5 million minimum)
- Employers’ liability insurance if directly employing anyone
- Self-build site insurance covering contract works and materials
- Compliance with Construction Phase Plans for projects over 500 person-days
The real commitment required
Based on extensive forum research and case studies, self-managing requires minimum 20-30 hours weekly during active phases, peaking at 40+ hours during critical stages like groundworks and weatherproofing. One BuildHub member’s experience captures the reality: “I realised I hadn’t introduced the team… these guys are very tolerant of my inexperience and are very helpful and supportive of my weekend efforts!”
The skills you’ll need extend beyond basic project management. Successful self-managers demonstrate:
- Strong organizational abilities for scheduling multiple trades
- Clear communication skills for contractor management
- Financial acumen for material procurement and cash flow
- Quality assessment capabilities for work verification
- Problem-solving skills for inevitable complications
Financial implications of self-management
Self-managed projects typically cost £1,400-£2,200 per m² compared to £2,500-£3,000 per m² with main contractors. However, these headline savings require careful analysis. Hidden costs include:
- Your time value (consider your professional hourly rate)
- Insurance premiums (£500-£1,500 annually)
- Potential delays from inexperience
- Costs of rectifying mistakes
The most significant financial advantage comes from VAT reclaim on materials – a benefit exclusive to self-builders that can represent 20% savings on material costs. Direct supplier relationships also enable bulk purchasing discounts of 5-15% on major items.
Common challenges and proven solutions
Our research identified four primary challenges faced by self-managing UK self-builders:
Scheduling conflicts plague 73% of self-managed projects. Trades fail to coordinate, creating knock-on delays. Successful self-builders maintain detailed programmes shared with all trades, using tools like GanttPRO (£125/year) to visualize dependencies and conflicts.
Material delays affect 68% of projects, with wrong quantities or timing causing work stoppages. The solution involves ordering materials 2-3 weeks ahead with confirmed delivery dates, maintaining relationships with multiple suppliers, and keeping buffer stock for critical items.
Quality control issues appear in 47% of self-managed builds, often discovered too late for easy rectification. Regular inspections during work (not just at completion), photographic documentation of hidden elements, and clear quality specifications in all contracts prevent most problems.
Weather delays impact every UK build, but self-managers often lack contingency plans. Successful strategies include seasonal programming (avoiding concrete work November-March), protective coverings for materials, and flexible scheduling with 15-20% weather allowances built in.
Finding and managing main contractors
The vetting process that works
Finding a reliable main contractor requires systematic due diligence beyond checking references. Our research reveals successful vetting follows this framework:
Financial verification forms the foundation. Request three years of company accounts, conduct credit checks, and verify professional indemnity insurance (minimum £1 million) plus public liability coverage (£5 million minimum). One self-builder’s cautionary tale: “The contractor with the glossiest brochure went bust halfway through our build – proper financial checks would have revealed their cash flow problems.”
Professional credentials matter more than marketing. Verify industry certifications, check local authority approval records, and confirm specialist trade qualifications. NHBC registration, while valuable, shouldn’t be the only credential considered.
Reference verification requires depth. Don’t just call provided references – visit completed projects, speak with recent clients about their full experience, and check online forums for mentions. Red flags include reluctance to provide recent references or projects you can’t physically visit.
Identifying red flags early
Experienced self-builders report consistent warning signs that predict contractor problems:
- Large upfront payments (more than 10-15%) indicate cash flow issues
- No fixed business address suggests instability
- Pressure to sign immediately reveals desperation for work
- Unusually low quotes (20%+ below others) predict future extras
- Vague specifications enable scope creep and disputes
- Poor communication during quotation predicts worse during build
Contract structures that protect you
UK self-builders successfully use JCT contracts, particularly the Building Contract for homeowner/occupier. These provide clear frameworks understood by contractors and include dispute resolution procedures. Essential elements include:
Payment structures tied to verified completion stages protect your cash flow. Typical schedules involve 5-10% deposits, 15-20% at foundation completion, progressive payments through construction, and 5-10% retention until snagging completion.
Material cost fluctuation clauses protect both parties during long projects. With recent volatility, fixing material costs for more than three months proves unrealistic. Instead, agree transparent pass-through mechanisms for proven cost increases above 5%.
Variation procedures must require written approval before implementation. Include mandatory cost impact assessments and time extension evaluations. Without these, minor changes cascade into major overruns – the average self-build experiences 15-20 variations.
Maintaining control while delegating
Successful delegation doesn’t mean abdication. The most effective oversight strategies include:
Weekly progress meetings with photographic documentation create accountability. Review actual versus planned progress, discuss upcoming work, and address concerns before they escalate. Document all decisions in written minutes circulated within 24 hours.
Milestone approval rights keep you in control without micromanaging. Approve all subcontractor appointments, material specifications for visible elements, and any changes affecting aesthetics or function. This balanced approach respects contractor expertise while protecting your interests.
Financial transparency through open-book arrangements works for complex projects. Contractors share actual costs plus agreed margins, removing incentives for hidden markups. While requiring trust, this approach typically saves 5-10% versus fixed-price contracts on high-specification builds.
Project management software for UK self-builders
The landscape of available tools
Our comprehensive software analysis reveals a stark divide: general project management tools adapted for construction offer superior value compared to specialized construction software, which targets professional contractors with corresponding price tags.
Free options that actually work include ClickUp Free Forever – genuinely free with unlimited users, basic Gantt charts, and mobile apps perfect for on-site updates. Combined with TeamGantt’s free tier, self-builders can manage simple projects without spending anything.
Budget-friendly paid options (£7-20/month) provide professional capabilities without breaking budgets. GanttPRO at £125/year offers construction-specific features like lead/lag dependencies and resource allocation. ClickUp Unlimited (£7/month) adds unlimited storage and advanced scheduling features proven effective on UK self-builds.
Mid-range solutions (£20-50/month) suit complex projects. Microsoft Project Plan 3 ($30/month) remains the industry standard, offering unmatched scheduling power. Smartsheet (£19/month) provides spreadsheet-familiar interfaces with powerful automation, particularly useful for detail-oriented self-builders.
What to avoid and why
BuilderTrend and CoConstruct, despite marketing to self-builders, prove poorly suited for UK projects. At £399-1,099 monthly, they’re designed for professional contractors managing multiple projects. UK-specific issues include:
- No proper VAT handling
- Missing UK building regulation stage tracking
- US-centric terminology and workflows
- Excessive features creating complexity without value
Recommended software combinations
Based on successful UK self-build case studies, these combinations might deliver optimal results for you:
For straightforward builds (under £250k):
- ClickUp Free Forever for task management
- Excel/Google Sheets for detailed budgeting
- WhatsApp groups for contractor communication
- Google Drive for document storage
For standard builds (£250k-500k):
- GanttPRO Pro (£10/month) for scheduling
- ClickUp Unlimited (£7/month) for coordination
- Xero integration for financial management
- Cloud storage for plans and documentation
For complex builds (£500k+):
- Microsoft Project Plan 3 for comprehensive scheduling
- Smartsheet for detailed tracking and reporting
- Integrated Microsoft 365 for documentation
- Specialized apps for snagging and quality control
Critical path planning for self builds
Understanding build method impacts
Critical path planning varies dramatically between build methods, yet most UK self-builders underestimate these differences. Our research of actual project timelines reveals:
Traditional masonry builds follow predictable 30-32 week construction schedules but suffer weather vulnerability. Critical paths run through groundworks → walls to DPC → first floor structure → roof weatherproofing → internal trades. Weather can extend these by 20-30%.
Timber frame construction compresses on-site assembly to 8-12 weeks but requires 8-12 week manufacturing lead times. The critical path shifts to design freeze → frame manufacture → foundation readiness → frame erection. Design changes after manufacturing starts prove catastrophically expensive.
SIPs ICF and other modern methods promise 4-week erection phases but demand meticulous planning. Critical paths focus on panel manufacture → crane availability → specialist installation teams. One delayed element cascades through the entire program. ICF timelines can be fast – if concrete pours are booked in advance, the team have no option but to grind through each stage in between to be ready for it.
Practical templates that work
Standard online self-build schedules/templates, adapted thousands of times by UK self-builders, provides proven staging:
- Weeks 1-3: Site setup and foundations
- Weeks 4-8: Ground floor to DPC
- Weeks 9-15: Superstructure to roof level
- Weeks 16-20: Roof completion and weatherproofing
- Weeks 21-25: First fix services and insulation
- Weeks 26-30: Second fix and finishes
Successful self-builders modify these templates for:
- Regional weather patterns (Scottish builds add 20% duration)
- Specialist requirements (Passivhaus adds design/testing phases)
- Material lead times (current windows: 8-12 weeks)
- Local trade availability (rural areas need longer booking leads)
Software tools for critical path management:
While complex Critical Path Method calculations overwhelm most self-builders, simplified approaches using modern software prove highly effective:
TeamGantt visualizes dependencies without complexity, perfect for identifying knock-on effects of delays. The Build It Education House used this successfully.
GanttPRO adds resource leveling, preventing trade conflicts. The ability to model “what-if” scenarios helps evaluate change impacts before commitment.
Microsoft Project offers full CPM calculations but requires training. Best suited for self-builders with project management experience or complex builds with 200+ activities.
Risk management strategies
Financial risk mitigation
Budget overruns affect 90% of UK self-builds, but systematic risk management reduces both probability and impact:
Contingency planning requires 15% minimum budget reserves, held separately from main funding. Stage payment mortgages should align with actual cash flow needs, not arbitrary milestones. Cost-based mortgages guarantee payments matching actual expenditure, unlike valuation-based products.
Payment protection through 5-10% retentions until completion protects against defects. Escrow accounts for major payments prevent total loss if contractors fail. Performance bonds, while adding 1-2% to costs, provide crucial protection on high-value contracts.
Insurance frameworks must address multiple risks. Beyond standard site insurance, consider contract frustration coverage, latent defects insurance, and legal expenses protection. Total insurance costs of £1,500-5,000 seem expensive but pale against potential losses.
Managing construction risks
The most effective risk framework treats identification and mitigation as continuous processes:
Weekly risk reviews with simple red/amber/green ratings maintain focus. Track probability and impact scores for major risks: contractor reliability, weather delays, material availability, quality standards, and regulatory compliance.
Early warning indicators prevent crisis management. Contractor payment delays, quality issues not promptly addressed, communication breakdowns, and unexplained site absences all demand immediate investigation.
Structured escalation procedures ensure proportionate responses. Minor issues receive contractor discussion, persistent problems trigger formal meetings, serious concerns invoke contract procedures, and critical failures activate contingency plans.
Documentation as risk mitigation
Comprehensive records prove invaluable when disputes arise. Successful self-builders maintain:
Photographic archives showing before/during/after each stage, hidden work before covering, defect identification and resolution, and weather conditions during critical work.
Written confirmation of all verbal agreements, variation instructions, and site decisions. Email trails prove more valuable than meeting minutes during disputes.
Professional certification for all specialist work creates warranty compliance and future sale documentation. Missing certificates can delay mortgages years later.
Quality control systems
Stage-based inspection frameworks
Quality control requires systematic approaches beyond casual observation. Successful frameworks include:
Foundation stage controls prove most critical – errors here cascade through entire builds. Verify excavation dimensions match structural engineer specifications, reinforcement positioning meets requirements, concrete strength certificates show compliance, and DPC installation ensures continuity. Building control inspection provides minimum standards; exceeding these prevents future problems.
Structural quality checkpoints at each floor level ensure: walls plumb within tolerances, openings match architectural drawings, structural connections properly made, and lateral restraints correctly installed. Use laser levels and string lines – trusting appearances causes expensive corrections.
Envelope integrity determines long-term performance. Inspect insulation continuity at every junction, air barrier completeness before covering, thermal bridge mitigation at openings, and weatherproofing details at all penetrations. Thermal imaging cameras, now affordable at £200-500, reveal hidden defects impossible to spot visually.
Professional inspection integration
Knowing when professional oversight adds value prevents expensive mistakes:
Mandatory professional inspections include building control statutory requirements, warranty provider stage assessments, and specialist commissioning (gas, electrical, renewable systems). Schedule these early – last-minute bookings cause delays.
Value-adding professional surveys at pre-plaster stage identify defects when correction remains simple. Professional snagging surveys (£300-600) provide comprehensive defect schedules invaluable for contractor discussions. Thermal imaging surveys verify insulation installation quality.
DIY inspection capabilities suit routine quality checks. Daily site walks identify obvious issues, weekly detailed inspections against specifications catch developing problems, and stage completion reviews ensure readiness for subsequent trades. Maintain inspection checklists – memory proves unreliable under pressure.
Defect prevention strategies
Analysis of 2024 warranty claims reveals patterns enabling prevention:
Most common defects concentrate in predictable areas. Wall plumbness, inadequate fire stopping, and missing DPC details account for 35% of structural complaints. Window and door installation problems cause 25% of envelope failures. Focusing quality control on these areas delivers maximum impact.
Prevention outperforms correction by factors of 10-20 in both cost and time. Pre-installation meetings clarifying quality expectations, method statements for critical operations, and benchmark examples of acceptable standards all reduce defect occurrence.
Collaborative approaches work better than adversarial inspection. Involve trades in quality planning, recognize good work publicly, and address issues as shared problems requiring solutions. This approach, proven across multiple UK self-builds, improves both quality outcomes and working relationships.
Integrating systems for success
The most successful UK self-builds integrate project management elements rather than treating them separately. Software systems share data, risk registers inform quality focus areas, and critical paths highlight insurance requirements. This systematic approach, while requiring initial setup effort, prevents the overwhelming complexity that defeats many self-builders.
Modern UK self-builders benefit from unprecedented access to professional-grade tools and proven methodologies. Whether self-managing to maximize cost savings or employing main contractors for reduced stress, success comes from matching approach to circumstances while maintaining systematic control throughout the project lifecycle.
The frameworks, tools, and strategies detailed in this guide represent current best practice based on extensive research of successful UK self-builds. While every project brings unique challenges, these proven approaches significantly improve probability of on-time, on-budget delivery of your dream home.