The landscape of UK self-build construction in 2025
Self-building in the UK has evolved dramatically from traditional brick-and-block construction to encompass innovative systems that promise faster builds, superior energy performance, and greater design flexibility. With construction costs averaging £2,200 per square metre and energy efficiency standards tightening under Part L 2021, choosing the right construction method has never been more critical. This comprehensive guide examines every major construction system available to UK self-builders, providing the transparent costs, real performance data, and practical insights that existing resources lack.
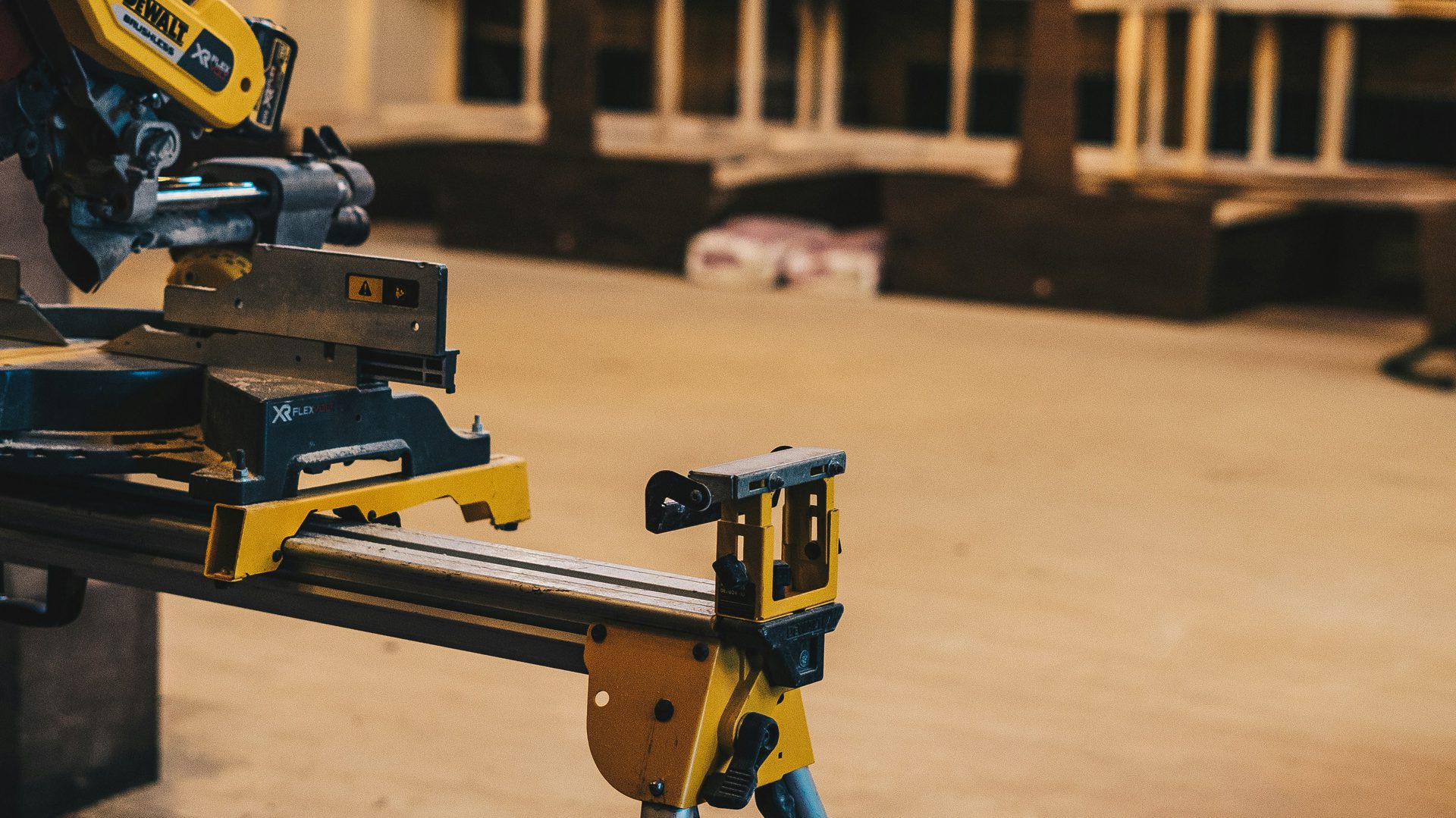
Timber frame systems dominate modern self-builds
Understanding the fundamental choice: stick-built versus panelized
Timber frame construction now accounts for 31.8% of UK self-builds, with panelised systems emerging as the clear winner over traditional stick-built approaches. Panelised systems deliver 30% faster construction than stick-built, reaching weathertight stage in just 5-6 days versus 7-8 days for stick-built frames. The precision-engineered panels manufactured in controlled factory environments eliminate weather delays and ensure consistent quality that warranty providers demand.
The cost premium for panelised systems – typically 15-20% more than stick-built initially – disappears when factoring in reduced labour time and superior quality control. Most critically, warranty providers often reject stick-built systems due to quality concerns, making panelised the only viable option for mortgaged builds. Frame Technologies achieves costs of £325-350 per square metre for standard specifications, while premium suppliers like Baufritz command up to £2,500 per square metre for their German-engineered systems.
Major UK suppliers deliver varied approaches and prices
The UK timber frame market offers distinct tiers of suppliers. Potton, operating from their St Neots show centre, provides comprehensive packages from £1,200 per square metre with generally positive customer reviews highlighting their expertise. Scandia-Hus brings Swedish technology to the UK market through their West Sussex facility, offering competitive pricing with supply-only or turnkey options. At the premium end, Border Oak specializes in post-and-beam construction combining traditional oak framing with modern SIPs panels.
Frame Technologies stands out for transparent pricing at £325-350 per square metre for frame-only supply, with their Suffolk cottage case study demonstrating a complete build at £2,059 per square metre. Their Herefordshire project achieved remarkable value at £1,000 per square metre through extensive DIY involvement, though this required significant personal labour input.
DIY feasibility requires realistic assessment
While timber frame attracts DIY enthusiasts, realistic skill assessment proves crucial. Essential carpentry skills include understanding mortise and tenon joints, reading technical drawings, and safe power tool operation. Tool investment ranges from £2,000-4,000, including critical items like circular saws (£200-600), routers (£150-400), and chain mortisers (£800-2,000).
Training opportunities abound, with Oak Heath offering comprehensive 5-day courses for £650 in the Brecon Beacons, covering complete frame construction techniques. The Centre for Alternative Technology provides similar training for £650 over 4 days in the Lake District. However, most self-builders find panelised systems with professional installation offer better value, eliminating warranty concerns while still allowing DIY involvement in finishing works.
Technical performance exceeds building regulations easily
Modern timber frame systems achieve U-values of 0.13-0.09 W/m²K in high-performance configurations, far exceeding the 0.18 W/m²K requirement for external walls. Airtightness below 1 air change per hour at 50Pa is routinely achievable, contributing to exceptional energy efficiency. The lightweight construction reduces foundation requirements while maintaining structural capability for buildings up to 6 storeys with proper engineering.
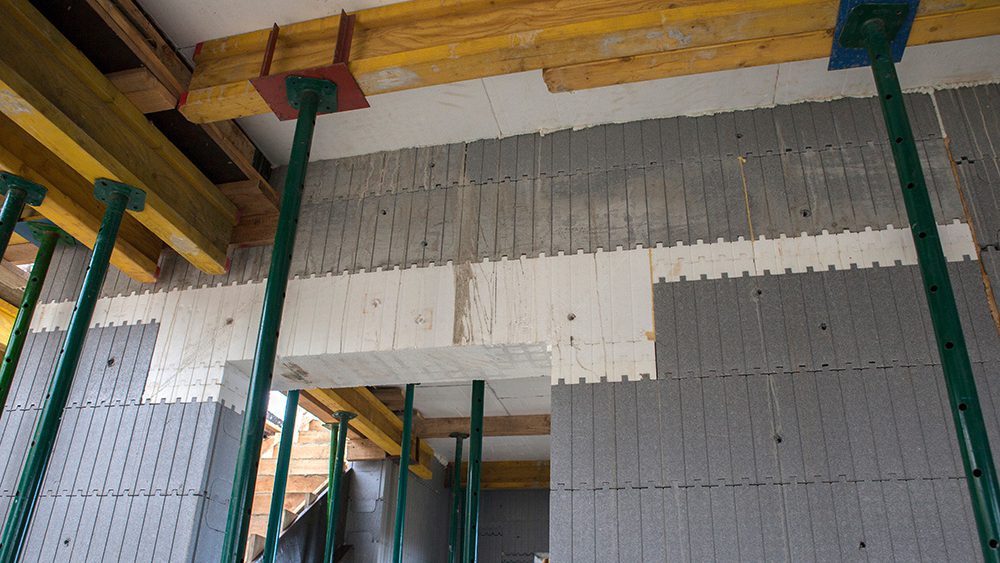
ICF construction delivers fortress-like performance
System comparisons reveal market evolution
Insulated Concrete Formwork (ICF) construction has matured significantly in the UK market. Nudura dominates with their patented hinged web technology, offering blocks at £35-45 per square metre that fold flat for shipping, reducing transport costs by 40%. Their 2438mm x 457mm blocks with 100-300mm core widths provide flexibility for various applications.
The market recently saw Logix ICF’s retirement in January 2025, replaced by Element ICF’s hybrid system. Thermohouse, manufactured in Ireland with UK distribution through Slough, offers complete building systems achieving Passivhaus standards. Integraspec’s reversible panel design at £35-38 per square metre reduces waste, while UK-manufactured Beco Wallform provides established reliability despite some reported blow-out issues on sites.
Training and certification prove essential
ICF success demands proper training, with Nudura’s mandatory one-day courses costing £150 including materials and certification. Jean-Marc Bouvier, with 30+ years ICF experience, leads training at locations including ICF Southern in West Sussex and ICF Central in Gloucestershire. The 8-hour online alternative provides flexibility, though hands-on experience remains invaluable.
True costs include long-term savings
While ICF commands a 10-25% premium over traditional construction, the financial analysis shifts dramatically when considering operational costs. Energy bill reductions of up to 70% translate to £140-190 monthly savings for a typical 2,000 square foot home, achieving payback within 5-8 years. Total build costs range from £120-180 per square metre for supply and fit, comparing favourably with brick-and-block cavity construction at £150-180 per square metre when considering the 40-60% faster construction time.
The Build It Education House demonstrated real costs with an 80m² basement at £985 per square metre, while the Clonshaugh social housing development showcased speed advantages with 36 units completed by just 4 installers in 6 weeks.
Performance metrics justify the investment
ICF construction achieves remarkable thermal performance with standard U-values of 0.26-0.30 W/m²K, easily meeting Part L requirements. Enhanced systems reach 0.10-0.18 W/m²K for Passivhaus applications. The concrete core’s thermal mass provides 324 hours to reach thermal equilibrium versus 60 hours for timber frame, delivering superior temperature stability and Part O overheating compliance.
Airtightness performance typically achieves 1-3 m³/hr/m² at 50Pa, with excellent installations reaching below 1 m³/hr/m². Fire resistance extends to 2-4 hours depending on wall thickness, while sound insulation proves ideal for party walls in semi-detached or terraced configurations.
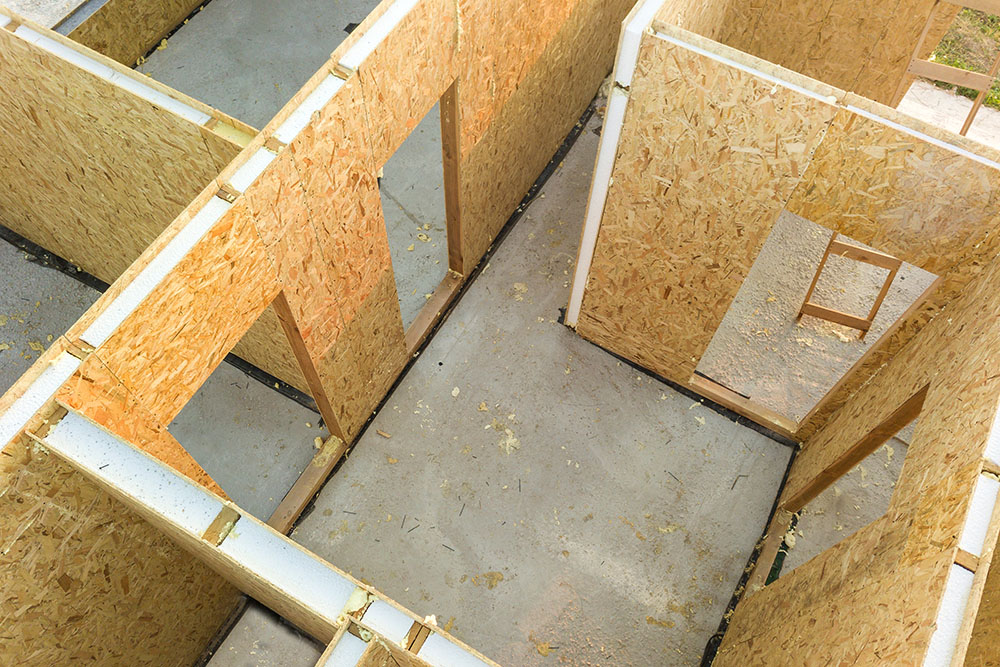
SIPs technology offers rapid precision construction
Technical specifications drive performance advantages
Structural Insulated Panels deliver factory-precision construction with remarkable speed. UK suppliers offer standard thicknesses from 96mm to 219mm, with Kingspan TEK’s 142mm and 172mm panels leading the market. The choice between EPS and PIR cores affects both cost and performance, with PIR achieving thermal conductivity of 0.022-0.028 W/mK versus EPS at 0.028 W/mK.
SIPS@Clays, as Kingspan TEK’s original delivery partner since 2003, exemplifies the comprehensive service approach with design, fabrication, and erection capabilities. Their Build It Awards 2024 win and Grand Designs features demonstrate proven excellence. Material costs range from £80-130 per square metre for basic EPS panels to £100-150 for PIR panels, with complete wall systems averaging £154 per square metre.
Installation demands precision but delivers speed
SIPs installation requires careful planning but rewards with exceptional speed – shell erection typically completes in 5-7 days with structures weathertight within days of delivery. Critical success factors include foundation accuracy within millimetres, proper lifting equipment (mobile crane essential for roof panels), and meticulous attention to airtightness at panel joints.
The installation process follows clear steps: foundation preparation with exact tolerances, panel positioning using telehandlers for walls and cranes for roofs, junction sealing with specialized tapes, and careful integration of services. Professional installation teams prove essential for warranty compliance, though smaller panels under 8×8 feet allow some DIY involvement.
Performance data validates the investment
SIPs consistently deliver exceptional performance metrics. Wall U-values range from 0.18-0.14 W/m²K for 142mm PIR panels to 0.11-0.15 W/m²K for 172mm versions, comfortably exceeding Building Regulations. Airtightness achievements of 0.57-0.84 m³/hr/m² at 50Pa rank among the best of any construction method, with 5 m³/hr routinely achievable versus the 10 m³/hr regulatory requirement.
Real projects demonstrate this performance translates to EPC ratings of A97, with 50% better energy efficiency than traditional timber frame. The excellent airtightness makes mechanical ventilation with heat recovery (MVHR) particularly effective, contributing to Passivhaus standard achievement on numerous projects.
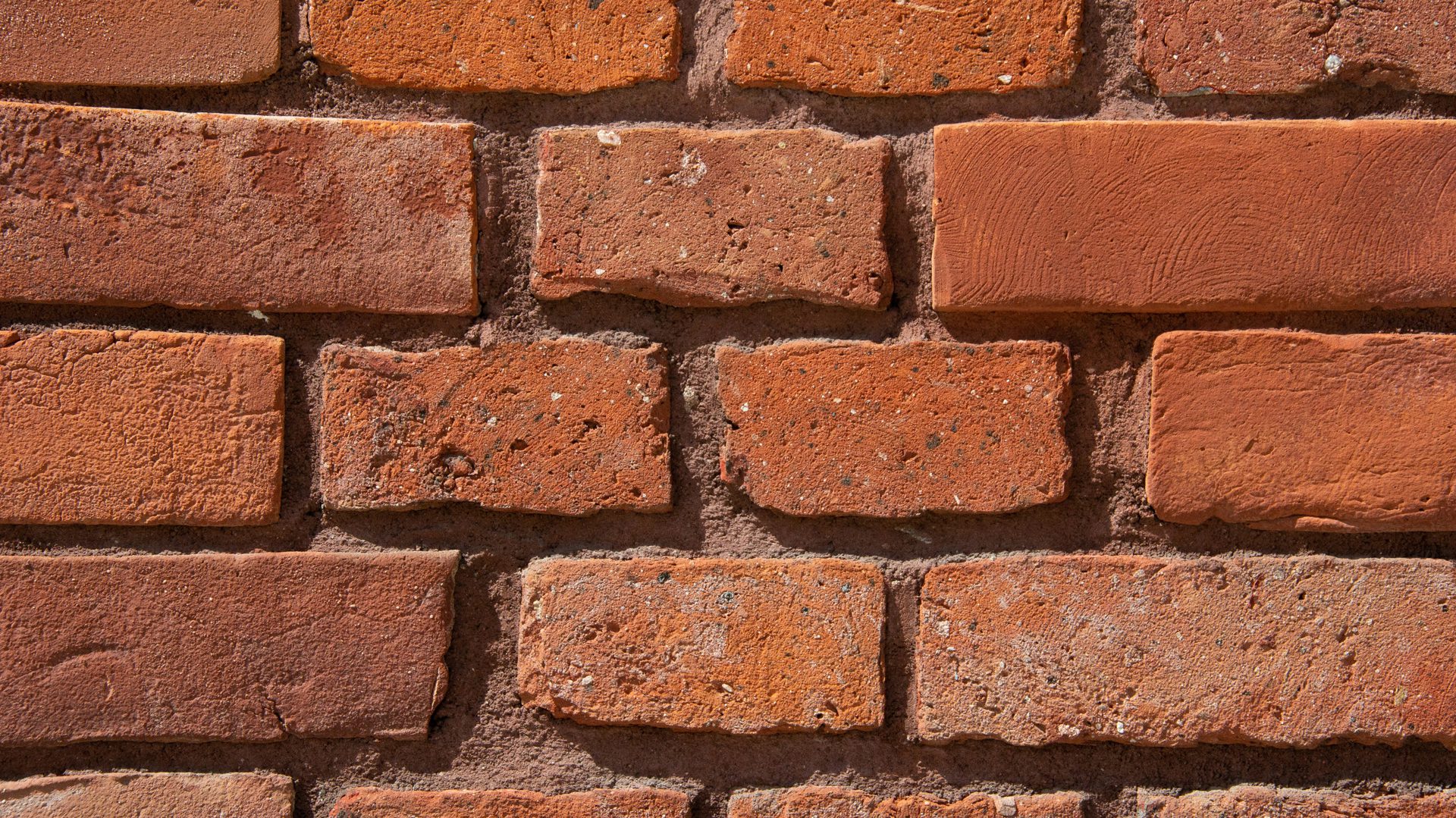
Traditional masonry evolves with modern techniques
Thin joint systems revolutionize blockwork
Modern masonry has transformed through thin joint technology, with H+H Celcon, Thermalite, and Tarmac Durox offering precision-manufactured blocks achieving ±1mm tolerances. These systems deliver 2-3mm joint thickness versus traditional 10mm joints, with mortar setting in 1-2 hours rather than 24 hours. The result: storey-height walls achievable in a single day versus the traditional 1.5m daily limit.
A Calford Seaden study revealed thin joint systems cost 8% less than timber frame or SIPs at Code Level 3, with greater savings at higher performance levels due to reduced renewable energy requirements. The combination of material costs comparable to traditional masonry with halved construction programmes proves compelling for many self-builders.
Block selection affects everything from cost to comfort
The UK market offers diverse block options, each with distinct characteristics. Aircrete blocks from H+H Celcon range from Solar grade at 2.8N/mm² to Super Strength at 10.4N/mm², with thermal conductivity of 0.11-0.18 W/mK providing excellent insulation. At approximately £2-4 per block, aircrete delivers up to 80% recycled content with Class A1 non-combustible fire ratings.
Aggregate concrete blocks serve higher-strength applications with 7.3-35+ N/mm² capacity but sacrifice thermal performance. Porotherm clay blocks offer a compelling middle ground, achieving 10 N/mm² strength with superior thermal regulation through their multi-cellular structure, enabling 30-40m² daily laying rates – five times faster than traditional masonry.
Insulation strategies meet modern standards
Meeting Part L 2021’s stringent requirements demands sophisticated insulation approaches. Full-fill cavity insulation now requires minimum 150mm cavity width, with options including glass mineral wool (λ = 0.034-0.037 W/mK) or PIR boards (λ = 0.021-0.023 W/mK). The BBA certification ensures moisture protection while maintaining thermal performance.
External wall insulation (EWI) systems offer retrofit capability and eliminate thermal bridging, with complete systems costing £40-80 per square metre installed. Modern render systems complement these approaches, with silicone renders at £40-70 per square metre offering 25-year warranties and minimal maintenance requirements.
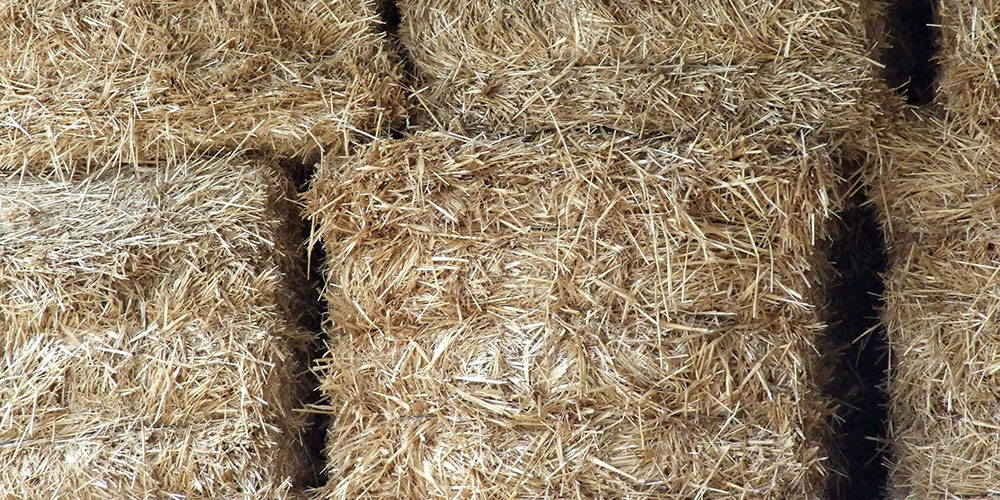
Alternative methods serve specialist niches
Straw bale construction proves surprisingly viable
Despite perceptions, straw bale construction offers genuine viability for committed self-builders. UK costs range from £111-140 per square foot (£1,194-1,507 per square metre), though the Somerset case study achieved £744 per square metre through extensive DIY involvement. The School of Natural Building provides essential training, with Barbara Jones’s technical guide enabling Building Regulations compliance.
Construction bales cost approximately £1,000 for 310 bales sufficient for a modest home, with wall systems representing only 15% of total build cost. While achieving excellent thermal performance far exceeding Building Regulations, the labour-intensive nature and mortgage challenges limit mainstream adoption. Ecology Building Society remains the primary lending option for these projects.
Hempcrete bridges sustainability and performance
Hempcrete construction has gained credibility through major commercial applications including Marks & Spencer supermarkets and the Science Museum archive. UK Hempcrete Ltd leads the market, with hempcrete blocks costing £105-300+ per square metre depending on thickness. Total build costs of £1,800-2,200 per square metre match high-specification conventional construction.
The material achieves thermal conductivity of 0.06-0.07 W/mK with remarkable thermal phase shift up to 23.6 hours, providing natural temperature regulation. Combined insulation and thermal mass characteristics unique to hempcrete reduce mechanical system requirements, though the non-loadbearing nature requires timber or steel frame support.
Earth building modernizes ancient techniques
Traditional cob construction faces challenges meeting modern thermal standards, requiring over 1 metre thickness for Part L compliance. However, the EU-funded CobBauge project has developed four thermally-compliant recipes targeting sub-600mm wall thickness for commercial viability.
Material costs remain low at £3,000-6,000 for a small house’s clay, sand, straw, and gravel, with wall systems representing just 10-15% of total build cost. Rammed earth construction commands premium pricing at £450-750 per square metre due to formwork intensity, limiting adoption despite aesthetic appeal.
Steel frame fills specific residential niches
Light gauge steel framing serves projects requiring long spans or multi-storey capability. Costs range from £250-350 per square metre for frame and cladding, with companies like Steel Frame Solutions and Remagin offering comprehensive services. The 200-300m² house erected and weatherproofed in one week demonstrates speed advantages, though 8-week manufacturing lead times and upfront payment requirements demand careful planning.
Thermal bridging through steel requires careful detailing, with minimum 33% thermal resistance needed outside the frame. The low DIY potential and specialist installation requirements limit adoption to specific architectural needs.
Hybrid approaches can maximize advantages
Popular combinations solve real problems
Timber frame with brick cladding dominates UK hybrid construction, delivering traditional aesthetics with modern performance. Special cavity wall ties accommodate differential movement while maintaining structural integrity. This approach enables the variety of brick types and patterns British planning authorities favour while capturing timber frame’s speed and efficiency benefits.
ICF ground floors with timber frame uppers serve sites requiring robust foundations or basement construction. ICF’s R-23.5 insulation value versus R-8.8 for typical batt insulation provides exceptional ground floor performance, while timber frame uppers reduce weight and cost. This combination particularly suits sloping sites or flood-risk areas requiring elevated living spaces.
Technical challenges demand careful design
Successful hybrid construction requires meticulous attention to connection details. Movement joints beneath all openings prove critical, with strategic placement at eaves, verges, and material transitions. Thermal bridging at system interfaces demands continuous insulation design with calculated thermal breaks to prevent condensation and heat loss.
The NHBC requires timber frame certification by qualified engineers with minimum 3 years’ experience, independent of the original designer. Structural Timber Association Assure scheme Gold level members can provide alternative certification, ensuring proper load transfer through carefully designed connection systems.
Cost implications vary by approach
Timber frame typically adds 15-20% over blockwork construction, translating to £12,000-17,500 for an average home. However, 20-30% faster construction delivers significant savings through reduced site preliminaries, weather independence, and earlier occupation. ICF foundations command 10-25% premiums but often eliminate expensive ground remediation.
Real projects demonstrate these calculations: the Suffolk timber frame with mixed cladding achieved modern aesthetics within traditional streetscapes, while the Oxfordshire self-build reached £1,000 per square metre through careful hybrid material selection and extensive DIY involvement.
Making informed decisions about your construction methods
The UK self-build construction landscape offers unprecedented choice, with each method serving specific needs and priorities. Traditional masonry with modern thin-joint systems suits those prioritizing thermal mass and acoustic performance while maintaining familiar construction approaches. Timber frame panelised systems deliver the optimal balance of speed, performance, and cost for most self-builders, explaining their 31.8% market share.
ICF construction justifies its premium through exceptional energy performance and durability, particularly for challenging sites or Passivhaus aspirations. SIPs technology serves those prioritizing speed and airtightness, with proven ability to achieve the highest energy ratings. Alternative methods like straw bale and hempcrete remain viable for committed eco-builders willing to navigate financing challenges.
Hybrid approaches increasingly dominate as self-builders recognize that combining systems can optimize performance while managing costs. The key lies in early engagement with experienced professionals who understand both individual materials and systems, and their integration challenges. With construction costs continuing to rise and energy standards tightening, the decision made today will impact both build costs and operational expenses for decades to come.